Collaborative piece, with Dominique Gaie.
A chance meeting, along the Rideau river; something clicks. We talk trees, bark, about what we do. I pot; she paints. Feel like decorating my vase? I ask. She looks at me, perplexed. I tell her about the vase I’d been making. You could sgrafitto your design. But, c’est quoi ça, sgrafitto? You’ll figure it out, I reply. And she did. But Oh no! She knew nothing about handling raw clay. As she worked, the rim broke. I carved away the broken rim. I asked: Still want to decorate this piece? Wabi-sabi? Take on board the mishaps along the way? She nods.
I had built the vase somedays earlier, using black stoneware clay, coating it with a patch of white porcelaneous slip, and another patch of ochre-coloured glaze. Using my tools, Dominique started creating trails through the slip, and through the glaze, down to the dark clay beneath.
Once bisque fired, I poured a satin white glaze on the inside, and used a spray gun to apply a very fine layer of transparent glaze over the outside surface.
My first collaborative piece; Dominique’s first time working with clay.
Slab-built; fired in oxidation, to cone 6.
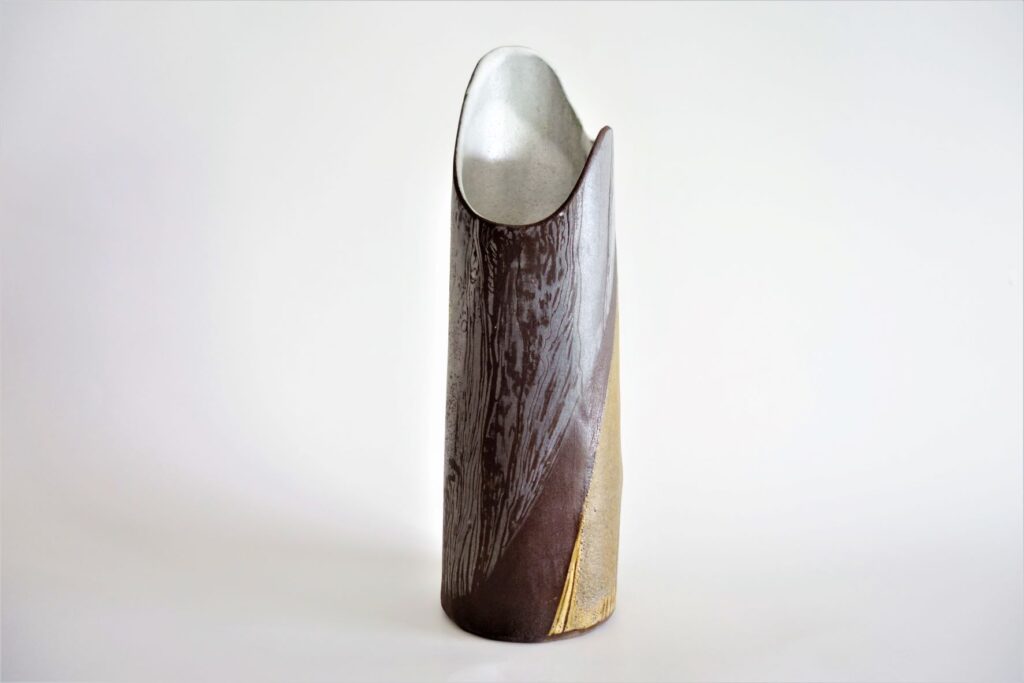
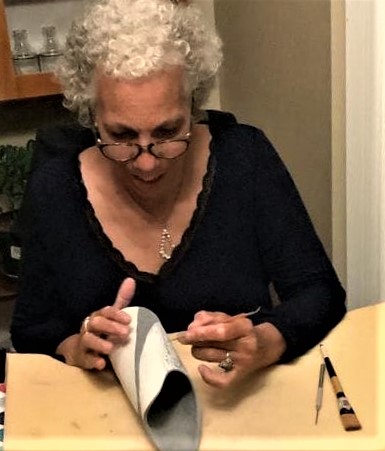